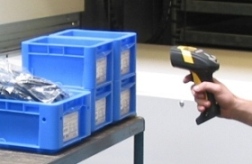
Wie kann eine Kanban Einführung ohne große Schwierigkeiten oder Probleme ablaufen, welche einfachen Kanban Regeln sind hilfreich?
Immer mehr Unternehmen erkennen die Vorteile und das Potenzial von «richtigen» Lean Kanban Pull Systemen im Gegensatz zur klassischen Steuerung mittels PPS-/ ERP System, die häufig der PUSH Systematik folgen.
Um den Materialfluss mit einem PULL System zu steuern wird sehr häufig das KANBAN Prinzip angewandt. Kanban ist prinzipiell leicht verständlich für die Mitarbeiter und hat den schönen Nebeneffekt, daß durch sogenannte «selbststeuernde Regelkreise» bei richtiger Anwendung ein recht geringer Aufwand im täglichen Betrieb anfällt, was zu deutlichen Einsparungen im administrativen Bereich führt.
Ohne Beachtung von Kanban Regeln bereitet die Einführung eines Kanban Systems manchmal Schwierigkeiten!
Aus diesem Grund haben wir unten einige typische Fehler bzw. Regeln bei der Kanban Einführung aufgeführt (sicherlich gibt es noch einiges mehr, was man falsch machen kann, aber wir denken dies sind ganz sicher die allerwichtigsten Regeln, denen man größte Beachtung schenken sollte!).
Desweiteren haben wir einige Ratschläge für Sie, die als Anregung dienen sollen, um die beschriebenen Fehler gleich von Anfang an zu vermeiden und Ihr Kanban System somit reibungslos einzuführen.
Selbstverständlich sind auch begleitende Maßnahmen zur Verbesserung und Optimierung der Produktions- und Logistikprozesse (KAIZEN) absolut zwingend notwendig, um die benötigten «Rahmenbedingungen» für ein Kanban System zu schaffen!
Hier nun die Liste typischer Fehler bei der Kanban Einführung:
Fehler 1: Keine richtige Auswahl der Kanban Teile
Das Artikelspektrum wurde nicht sauber analysiert und die Kriterien für Kanban-fähige Teile definiert.
Dadurch werden Teile in das Kanban System mit aufgenommen, die eigentlich nur schwer über Kanban zu steuern sind oder wenig Sinn machen.
Unser Tip: Starten Sie mit einer ABC-XYZ Analyse!
Zumindest eine ABC Analyse ist meistens recht schnell und einfach durchzuführen und hilft enorm dabei, ein «besseres Gefühl» für das eigene Artikelspektrum zu entwickeln.
Fehler 2: Kein Kanban Verantwortlicher
Es wurde keine verantwortliche Person festgelegt, die für die Pflege und Optimierung des Kanban Systems verantwortlich ist und die als Ansprechpartner für die Kollegen dient.
Unser Tip: Legen Sie unbedingt einen Kanban Verantwortlichen (Kanban Koordinator) fest!
Schicken Sie ihn auf Schulungen, geben Sie ihm die passenden lean Werkzeuge zum Kanban Management und natürlich auch die notwendige Unterstützung und Rückendeckung bei Problemen.
Speziell bei der Kanban Einführung ist dies kein «Halbtagesjob»!
Fehler 3: Keine solide Kanban Daten Basis
Die Daten werden in einem (komplexen/benutzerunfreundlichem) Excel-Sheet, ERP / MRP System oder ähnlichem Tool verwaltet. Die Verknüpfungen werden immer umfangreicher und kaum jemand kennt sich später noch damit aus.
Unser Tip: Stellen Sie das Kanban System von Beginn an auf eine solide Kanban freundliche Daten Basis, damit eine klare Struktur vorhanden ist und somit die Aufwände zur Datenpflege, Auswertung und Drucken der Kanban Karten möglichst gering sind. Verschwenden Sie also keine Zeit mit der Mißachtung einfachster lean Basis Prinzipien oder «sogenannten» Kanban MRP / ERP Add-Ons, hier erwarten sie garantiert keine Allheilmittel!
Ihre Mitarbeiter werden es Ihnen danken und die Kanban Einführung wird wesentlich reibungsloser verlaufen, wenn sie ihnen die richtigen Hilfsmittel von Anfang an in die Hand geben!
Fehler 4: Keine standardisierten Kanban Karten
Die Kanban Karten wurden mir Word, Excel oder sonst irgendwie erstellt und haben kein Standardformat bzw. die Daten sind unvollständig oder fehlerhaft.
Unser Tip: Legen Sie einen Standard für die Kanban Karten fest
(ggfs. unterschiedliche Größen für unterschiedliche Kanban Behältertypen) und sorgen Sie für einen schnellen und einfachen Druck der Kanban Karten ohne großen Aufwand.
Fehler 5: Die Losgrößen sind viel zu groß
wodurch eine riesige Anzahl an Kanban Karten entsteht, die in der Praxis nur schwer zu handhaben ist.
Auf die sonstigen negativen Aspekte von zu großen Losen wollen wir an dieser Stelle nicht eingehen!
Unser Tip: Arbeiten Sie an der kontinuierlichen Reduzierung der Losgrößen und der Rüstzeiten. Dies ist elementar wichtig für das Kanban System, für die Flexibilität und für den gesamten Produktionsprozeß.
Manchmal lassen sich bestehende Losgrößen auch ohne große Analyse einfach «kappen» und die Produktion läuft immer noch einwandfrei.
Fehler 6: Zu komplexe Kanban Prozesse
Die Prozesse sind viel zu komplex und dadurch fehleranfällig. Dies führt zu «verlorenen» Kanban Karten und einer schlechten Transparenz.
Unser Tip: Schaffen Sie einfache und klare Prozesse, die alle Mitarbeiter auch verstehen.
Definieren Sie klare Verantwortlichkeiten und transparente Abläufe in der Produktion (Kanban Sammelstellen, Visualisierung von Informationen, Kanban Regeln,…).
Fehler 7: Keine begleitenden KAIZEN Maßnahmen
Ein Kanban System deckt häufig bestehende Probleme schnell auf (schlechte Qualität, zu hohe Lose und Rüstzeiten etc. etc.), aber es wird nichts unternommen, um diese Probleme zu beheben und das notwendige Umfeld zu schaffen.
Unser Tip: Dokumentieren Sie die Probleme und Schwachstellen!
Diskutieren Sie die Punkte im Team und leiten Sie die notwendigen Maßnahmen und Projekte in die Wege!
Starten Sie zügig mit der Umsetzung und Optimierung!
Denken Sie daran, Kanban ist ein starkes Werkzeug,
aber es ist nur ein (LEAN) Puzzle- Teil und löst nicht alle Probleme automatisch!
Haben Sie weitere Fragen zur Einführung von KANBAN?
Unser letzter und bester Tip: Kontaktieren Sie uns, wir helfen Ihnen jederzeit gerne weiter!
LEAN / KANBAN
Klicken Sie auf das gewünschte Thema um mehr zu erfahren.